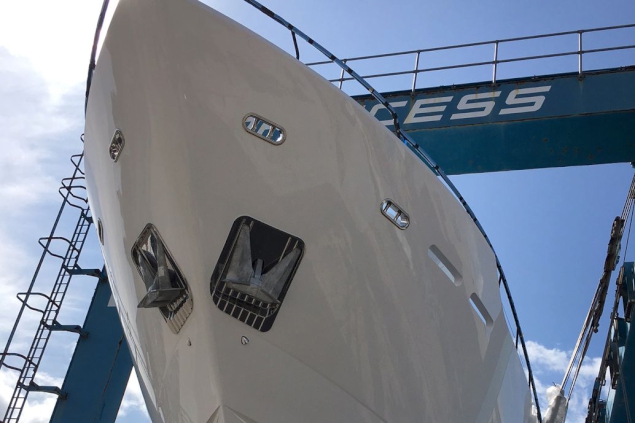
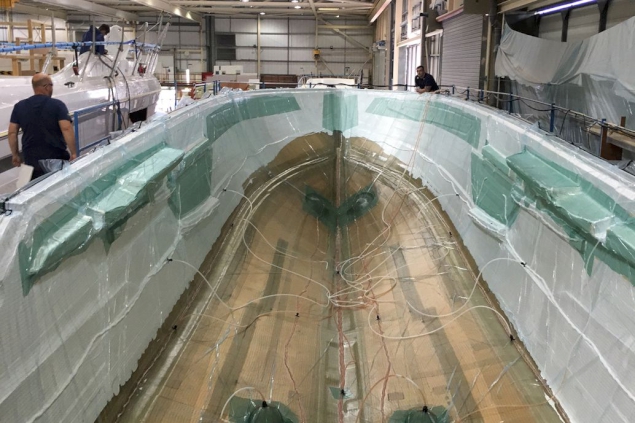
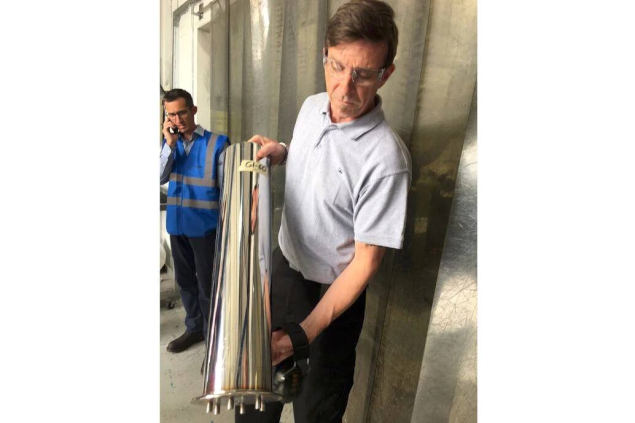
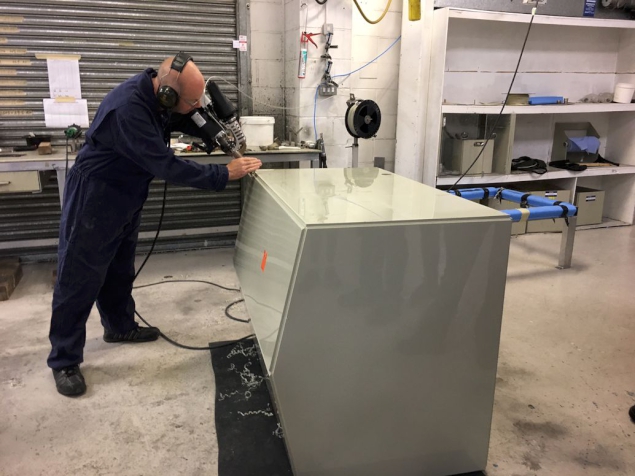
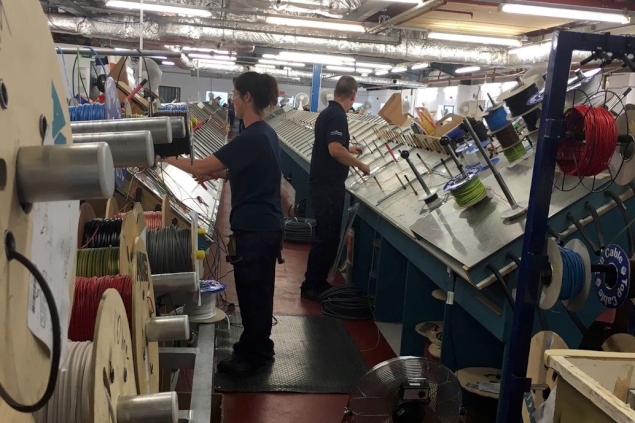
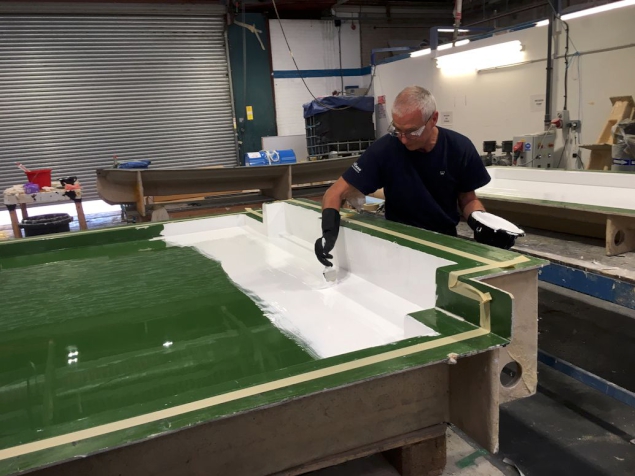
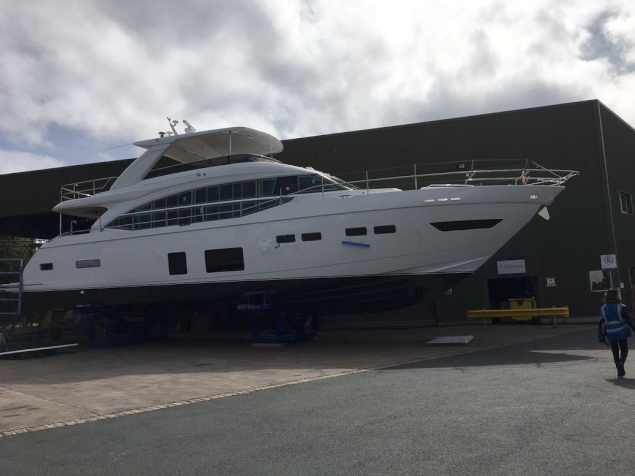
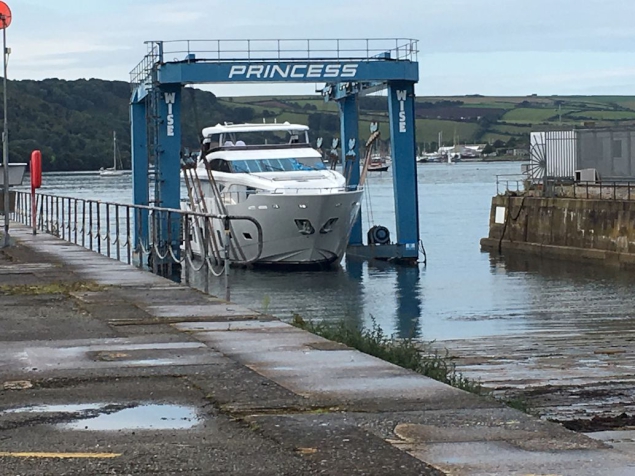
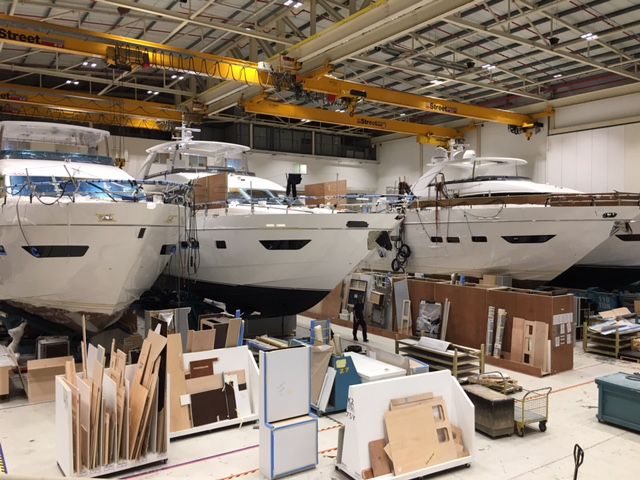
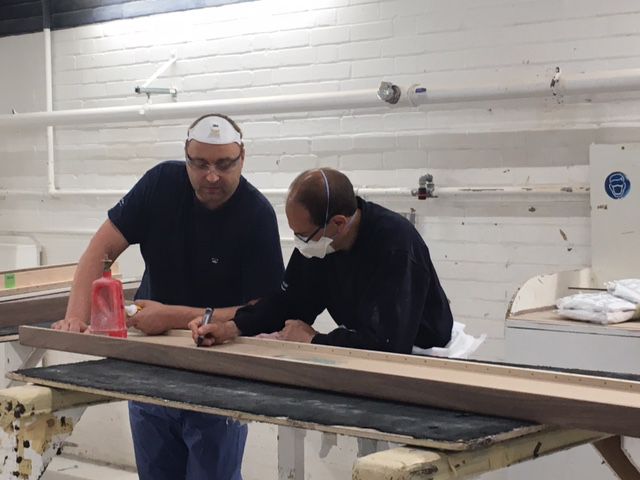
After 25 extraordinary years, JD Yachts will be closing its doors.
This has not been an easy decision—but it’s one we’ve made with deep reflection and immense pride in all that we’ve achieved. We set out to build a company grounded in trust, transparency, and a passion for getting people on the water. We believe we’ve done just that.
To our clients—some of whom have been with us from the very beginning—we owe everything. Your unwavering support and trust shaped our journey. Many of you returned to us time and again for your boating needs, and that loyalty became the foundation of our business. We’re honoured to have helped so many families and individuals realise their dreams of yachting across the UK and the Mediterranean.
To our industry colleagues, tradespeople, and the marinas who welcomed and supported our work—you made this possible. The collaborative spirit and shared commitment to excellence within the marine sector gave JD Yachts its wings. We always sought to drive business back into local trades and infrastructures, and we’re proud to have played a part in sustaining that ecosystem.
To our dedicated team—Toby Hawkins and Isabella O’Leary—thank you for your incredible contribution, professionalism, and commitment to our shared mission. You’ve been integral to our journey and success.
A special thank you to our families for your constant support, patience, and belief in us—especially through the demanding times. JD Yachts has always been about more than just boats; it’s been about people, partnerships, and heart.
The current business climate, especially for SMEs in the marine sector, has become increasingly complex and challenging—particularly in relation to post-Brexit trade regulations and the double taxation of vessels between the UK and EU. These conditions have made it nearly impossible to scale sustainably or operate competitively abroad. We believe it’s important to acknowledge how much the industry has changed—and how vital it is to protect what was once a thriving cornerstone of Britain’s maritime heritage.
As we close this chapter, we do so with enormous gratitude for every client, colleague, and friend we’ve met along the way. The memories, the adventures, and the trust you placed in us will stay with us forever.
Thank you for letting JD Yachts be part of your story. We are proud of the legacy we leave behind.
With heartfelt thanks,
Darren & Justin